
by Amanda Siegfried
It’s clean; it’s sustainable; and it’s abundant from the Gulf of Mexico to the West Texas plains. UT Dallas engineers are riding a tailwind as their work propels innovations that will help increase wind’s role as a power player in the Lone Star State.
Take a spring drive along Interstate 20 near Sweetwater in West Texas, and you’ll see them, towering above the bluebonnet-strewn landscape like pinwheels in a giant’s garden.
The Roscoe Wind Farm in Nolan County is one of the world’s largest-capacity wind farms, with more than 600 wind turbines generating enough electricity to power over 250,000 Texas homes.
For a state nearly synonymous with oil and natural gas production, Texas leads the nation in the number of wind turbines — more than 13,000 — and in its capacity to generate electricity from wind. In 2018 that was enough to power more than 7 million homes.
Wind not only generates power, but it also fuels jobs and economic development in the Lone Star State. According to the American Wind Energy Association, Texas leads the nation with more than 25,000 people employed in the wind industry, and it has 46 manufacturing facilities that produce products and supply raw components.
As the wind business booms — not only in Texas but across the country and worldwide — engineers at The University of Texas at Dallas are driving innovation in wind-turbine design and efficiency, propelled by new research facilities and a state-of-the-art building that provide opportunities for students to learn and for industry partners to boost their bottom lines.

WindSTAR
Texas’ wind-friendly terrain sits at the south end of a blustery corridor that stretches from the Great Plains into Canada, an ideal environment for the huge, three-bladed whirligigs.
Likewise, UT Dallas’ Department of Mechanical Engineering is well-positioned both geographically and with the right blend of faculty expertise to meet the challenges facing the wind industry.
Much of the University’s wind-energy-related research falls under the umbrella of the Wind Energy Science, Technology, and Research Industry/University Cooperative Research Center, or WindSTAR. Established in 2014 in collaboration with the University of Massachusetts Lowell, WindSTAR is one of 91 such cooperative centers funded by the National Science Foundation and the only one devoted to wind energy.
WindSTAR currently has 13 fee-paying industry members who work closely with academic researchers to identify projects and problems of interest.
“We are doing user-inspired research driven by a need, as opposed to fundamental research driven by curiosity,” said Dr. Mario Rotea, head of mechanical engineering at UT Dallas and co-director of WindSTAR. “The potential for wind energy is tremendous. But realizing this potential requires a coherent industry-relevant research and development program that involves industry, academia and government.”
Threefold Approach
Within WindSTAR, UT Dallas engineers and their students work collaboratively in three broad areas of research that intersect and inform one another: data gathering and analysis, computational fluid dynamics, and design of the control systems that operate turbines.
Combined, these efforts reveal ways to improve efficiency, performance and reliability, from the single turbine level to the scale of large wind farms.
Wind turbines are designed in the absence of detailed information about their ultimate installation location or configuration. So within each machine, sophisticated control systems and software adjust the pitch, yaw and speed of the blades and rotors in order to optimize performance for a given situation or environment.
Rotea’s research focuses on developing control systems that can automatically adapt the movement and orientation of turbines to their home conditions.
For example, turbines that end up in uneven or rough terrain will face wind patterns that are different from those in a flat, open area. In addition, a turbine’s placement within hundreds on a large wind farm can dictate how it will need to move: The rotating blades of a “lead” turbine produce ripples, waves and other disturbances in the air that can affect and interfere with air around turbines downstream, much like the wake of one boat can affect a boat behind it.
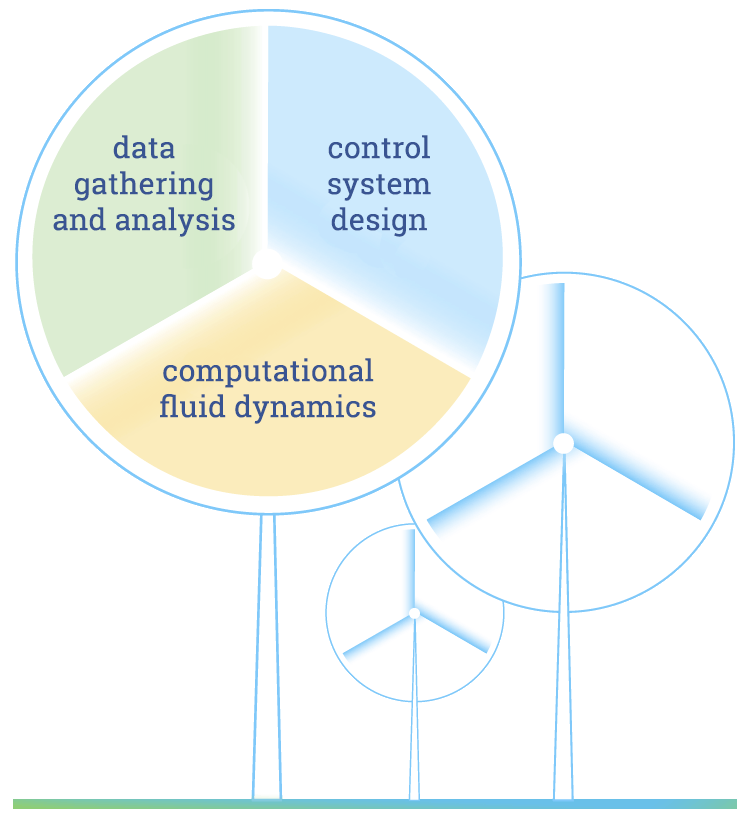
“The control system on each machine is automated and designed to respond in real time to changing conditions,” said Rotea, who is the Erik Jonsson Chair in the Erik Jonsson School of Engineering and Computer Science. “The system must adjust each turbine’s orientation in order to extract maximum power from the wind while not putting too much strain on any individual turbine.”
Rotea’s work is informed by that of his colleagues who combine field data with expertise in computational fluid dynamics. (From a mathematics and engineering standpoint, moving air and moving liquid are both treated as fluids.)
Dr. Giacomo Valerio Iungo, assistant professor of mechanical engineering, takes students and mobile equipment to a wind farm in North Texas to collect data. Measurement-taking involves light detection and ranging equipment, or LiDAR, which is similar to radar but uses light instead of radio waves. The technology directs pulsed laser beams toward a moving wind turbine and then picks up the reflection off of particles moving in the turbulent air.
“As the laser scans and bounces off of the moving air particles, we get information that can then be processed to give us wind speeds and direction,” Iungo said.
Data from such measurement campaigns is used by Dr. Stefano Leonardi, associate professor of mechanical engineering, in his complex computer models and high-fidelity simulations, which also incorporate information from Rotea’s control system work.
For example, Leonardi is investigating how much power is lost per turbine when the wake from one wind turbine interacts with another. Wind-farm configurations can cause up to 20% of lost production every year, according to the U.S. Department of Energy.
To measure the power production of each turbine and find potentially more efficient configurations, Leonardi’s research group runs their data-intensive simulations on high-performance computers at the Texas Advanced Computing Center at UT Austin. Information from such research could affect future wind-farm layouts and provide more accurate predictions of how much power is generated every year from a wind power plant.
“This collaboration is very fruitful,” Rotea said. “Dr. Iungo collects and analyzes field data; Dr. Leonardi uses some of that data to validate his computer models; and I inject the control systems. All of this combined can tell us what works in terms of improving the performance of a wind farm.”
Industry Benefits
“The time is right to leverage our investments in this field, to make Texas an even greater state for wind power in particular and wind engineering in general.”
Dr. Richard C. Benson
UT Dallas President
Companies involved in WindSTAR gain access to UT Dallas research and advanced facilities, as well as student projects focused on industry-driven needs. Industry partners range from turbine manufacturers to owner/operators to component and service providers.
Results from UT Dallas projects have provided valuable preliminary data to WindSTAR partners who then use that information to apply for federal grants. A recent WindSTAR collaboration with center member Aquanis resulted in just such an award.
Aquanis is a Rhode Island-based company that makes plasma actuators, which modify the air flow over the turbine blades, enabling them to instantly react to changes in the wind. This advanced control system reduces the cost of wind energy by making wind turbines more durable and eventually allowing blades to be built with less material.
UT Dallas engineers worked on a project with Aquanis to gather data on using plasma to reduce mechanical loads on blades at high wind speeds. The company used that data in a funding proposal, and in 2018 won a grant from the Department of Energy’s Advanced Research Projects Agency-Energy (ARPA-E) to increase the power output of wind turbines without increasing the mechanical loads.
“For an investment of about $30,000, Aquanis received $3.5 million, and UT Dallas got about $1.4 million to continue our research efforts,” Rotea said. “That’s a phenomenal return on investment for this company.
“This industry/university cooperative research center is an example of how UT Dallas has become part of an effort that has tremendous value to the innovation engine in this country. The end result will be new technologies for wind-power diagnostics, new control systems for improved reliability and energy capture, and graduates who are ready to take the lead in the field.”
In 2018, power generated from wind in Texas avoided 54 million metric tons of carbon dioxide emissions.
American Wind Energy Association
Everything’s Bigger in Texas
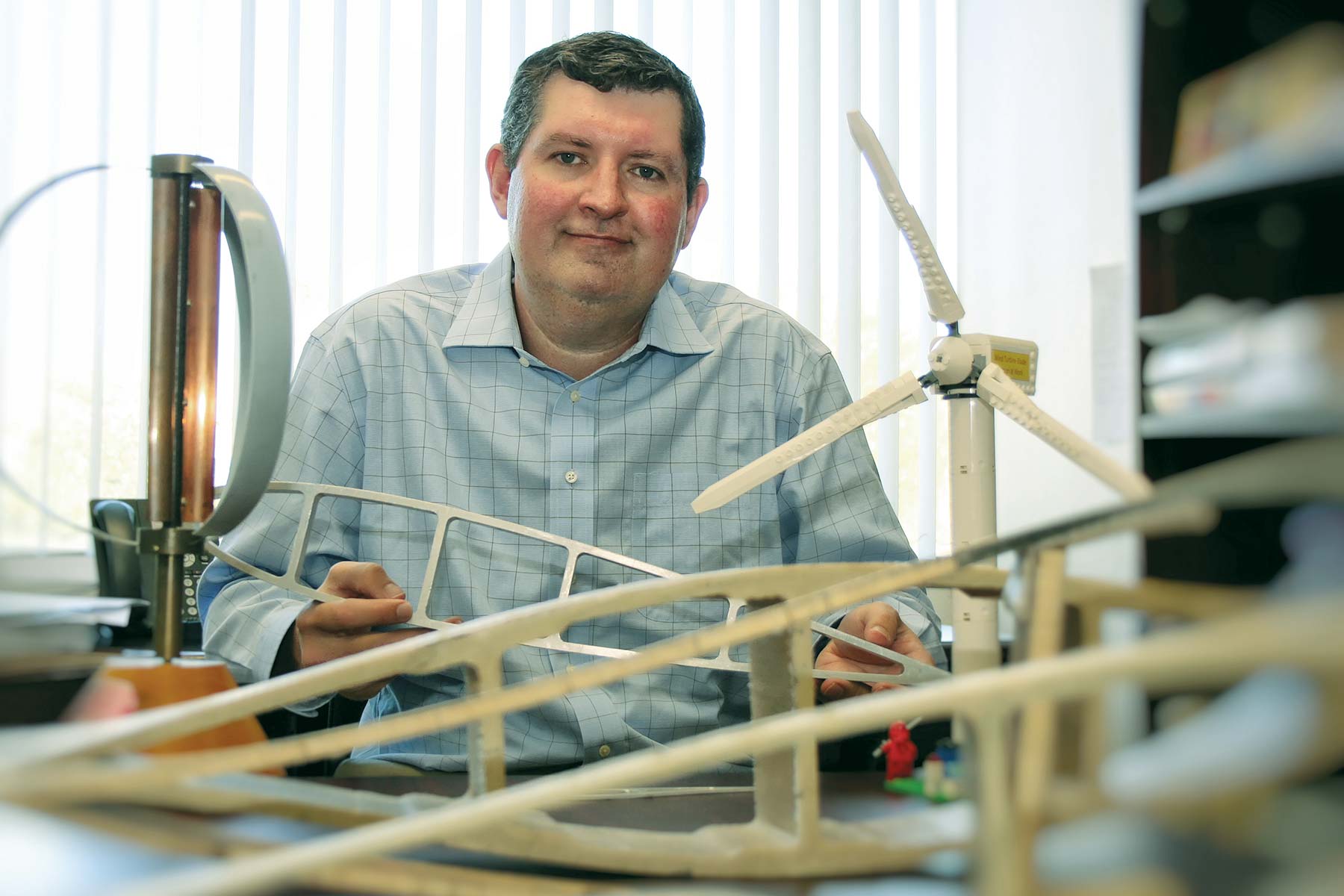
An industrial wind turbine can reach over 300 feet high, from the ground to the tip of an upstretched blade. That’s taller than the Statue of Liberty. Laid sideways, it would be approximately the length of a football field.
Dr. Todd Griffith, associate professor of mechanical engineering, has even grander designs in mind for the growing industry. He and his collaborators are developing the world’s biggest wind-turbine blades, inspired by an unusual source: palm trees.
“Our design is inspired by palm trees — how resilient they are when powerful winds blow,” Griffith said. “The fronds are flexible; they fold up in hurricane-force winds for protection. When they unfold, they’re fine. I wondered whether we could use that concept in a wind turbine.”
Before joining the faculty of the Jonsson School in 2017, Griffith was a principal member of the technical staff and offshore wind technical lead at Sandia National Laboratories’ Wind Energy Technologies Department. He has been a key member of a multi-institutional collaboration, led by the University of Virginia, to design and build a 50-megawatt offshore wind turbine roughly six times more powerful than the biggest one on record off the coast of Scotland.
Funded by a grant from ARPA-E, the collaboration also includes researchers at the University of Illinois at Urbana-Champaign, University of Colorado Boulder, Colorado School of Mines and the National Renewable Energy Laboratory (NREL).
Since arriving at UT Dallas, Griffith has continued his role on the project, working on the designs of next-generation blades over 750 feet long. Typical blades are about one-quarter that size.
“We’re designing the world’s largest wind turbine,” Griffith said. “Where else would you do it but Texas? Everything is bigger in Texas.”
“We’re designing the world’s largest wind turbine. Where else would you do it but Texas?”
Dr. Todd Griffith
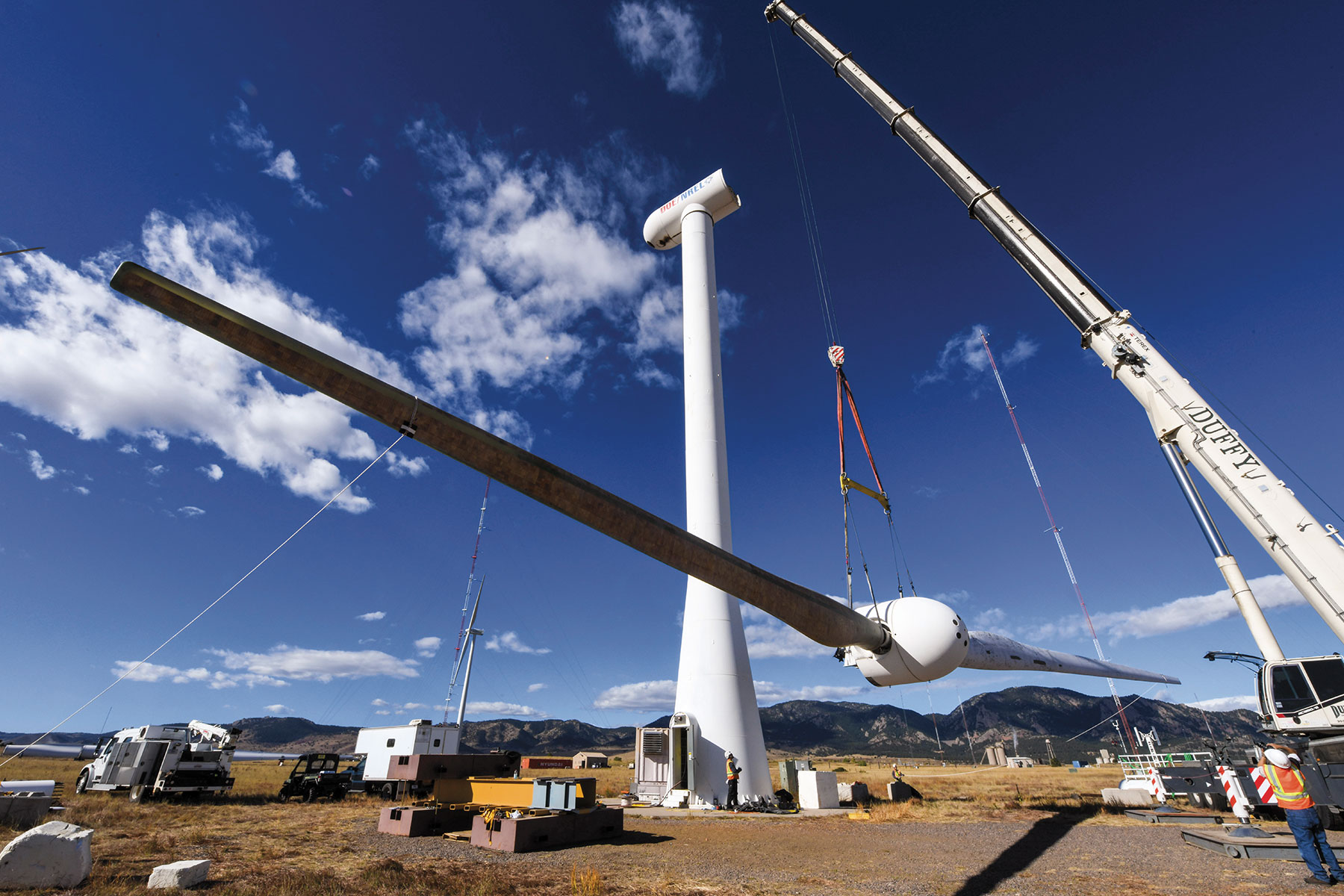
Gale-Force Strength
The massive turbine marks an about-face from conventional designs. The standard wind turbine is a three-bladed machine positioned with the blades facing incoming winds. The blades for the new concept, called a Segmented Ultralight Morphing Rotor (SUMR), would face downwind and would be tailored for offshore wind farms.
“If you build a wind turbine offshore, whether it’s in the Atlantic Ocean or the Gulf of Mexico, you’re going to have to deal with a hurricane event,” Griffith said. “Wind speeds can reach over 200 mph. That’s why we designed the turbine to perform the way palm trees perform and ride out a hurricane. They bend but don’t break.”
A hinge near the central hub of the turbine allows the blades to fully fold and collapse in hurricane-force winds. Each blade is built in four to five segments and assembled at the project site, eliminating the considerable challenge of transporting a single massive blade the length of two football fields on a truck.
“The cost of electricity dictates the success of a wind turbine design. Our approach to reducing electricity cost for the consumer is a significantly longer blade providing a much greater amount of energy extracted from the wind,” Griffith said. “Our UTD team is aiming for engineering a solution to make extreme-scale blades and low-cost offshore wind energy a reality.”
In October, Griffith’s research team began field testing a smaller prototype version of his team’s blade design on a 12-story turbine tower at NREL’s National Wind Technology Center in Golden, Colorado. Now, he’s planning to assess the prototype inside UT Dallas’ new subsonic wind tunnel and in his lab in the new Engineering and Computer Science West building, which opened in 2018 and contains high-ceilinged mechanical engineering labs that allow for testing of very large structures.
Award-Winning Building Offers Inside View of Engineering at Work
Four-stories high with 200,000 square feet of labs, classrooms and office space, the new Engineering and Computer Science West (ECSW) building at UT Dallas is inspired by student learning and advanced research. Designed by faculty and staff, the all-glass, modern exterior is sure to turn heads, but it is what’s inside that makes it a tangible lesson in engineering.
The $110 million facility, which opened in fall 2018, was supported by bonds and funding from various sources and primarily houses the Department of Mechanical Engineering. It includes a 300-seat auditorium, a retail food grab-and-go, a third-floor student lounge with a balcony and a landscaped courtyard with seating for study groups.
Special attention was paid to the building’s framework. All the piping and heating systems are visible, as are I-beams that support the load of the building, pipes for the sprinkler systems, even water chillers in the stairwells. Glass-windowed labs allow passers-by to see research, which includes energy, robotics and nanotechnology.
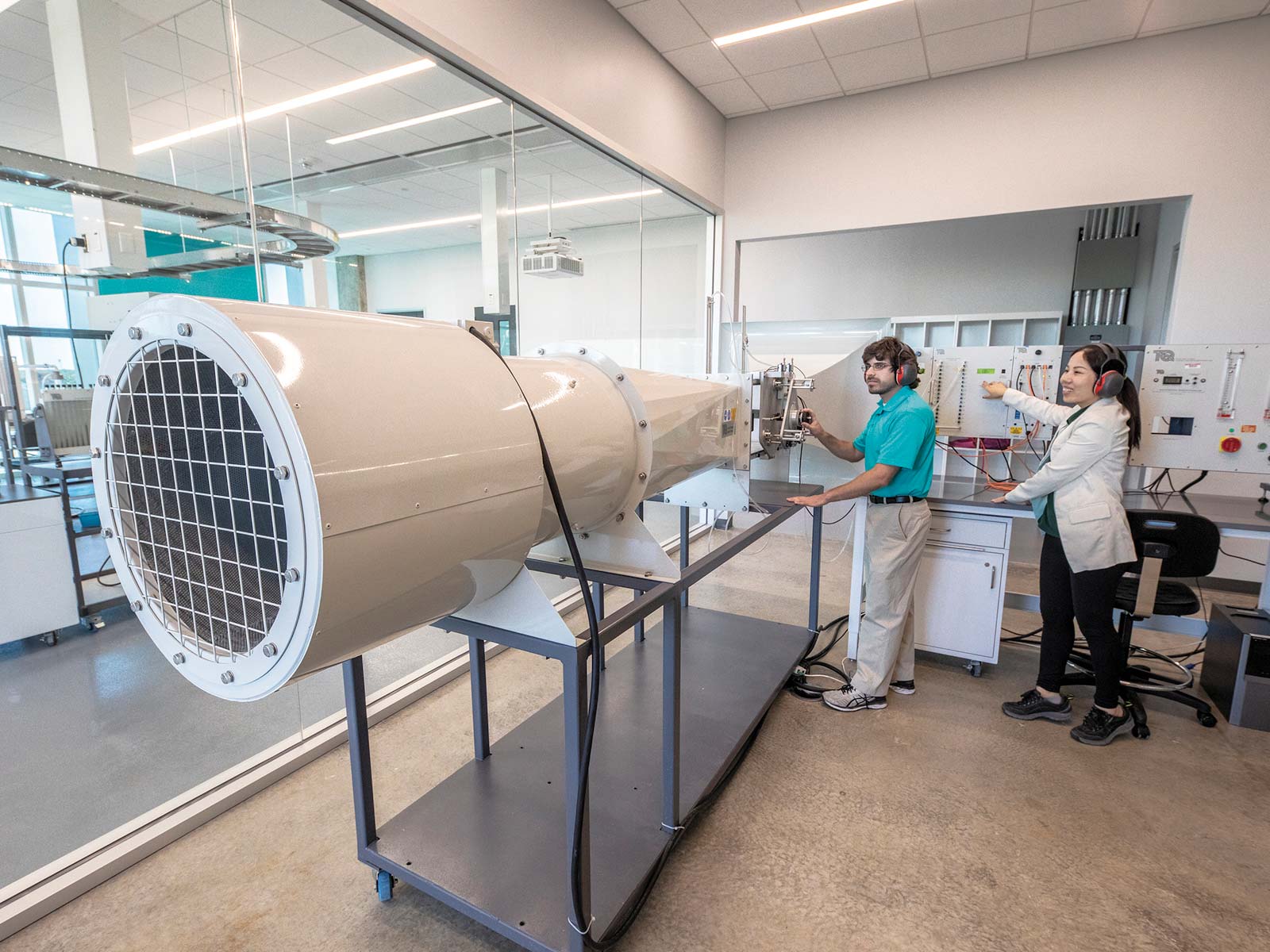
This year the building was awarded LEED Gold status by the U.S. Green Building Council, becoming the seventh building on the UT Dallas campus to earn LEED certification. LEED, or Leadership in Energy and Environmental Design, recognizes environmentally conscious construction.
Also, R&D Magazine presented ECSW with a 2019 Lab of the Year Award-Special Mention for Engineering Labs. This prestigious international competition recognizes innovative designs, materials and construction for laboratory and health care facilities.
“What distinguishes ECSW is that it is a student-centric building with plenty of space for students as well as exposed mechanicals to help educate mechanical engineers in 21st century building technologies,” said Dr. Mario Rotea, head of mechanical engineering.
BLAST Off
In August 2018 UT Dallas unveiled the newest investment in its wind-research portfolio. The Boundary Layer and Subsonic Tunnel, or BLAST, is an experimental testing facility that enhances the University’s existing wind-engineering capabilities, providing research and educational opportunities for faculty, students and industry partners.
The wind tunnel, shaped like an oblong doughnut, boasts a 26,000-pound fan that can create wind conditions similar to those in the atmosphere. Inside the tunnel, air flows around an anchored test object. The tunnel’s contraction cone takes a large volume of low-velocity air and reduces it to a small volume of high-velocity air without creating turbulence. A glass-paneled observing area allows 100 feet of visibility of the test area.
Researchers use the tunnel’s two test sections to study the effects of a range of wind speeds and turbulence levels.
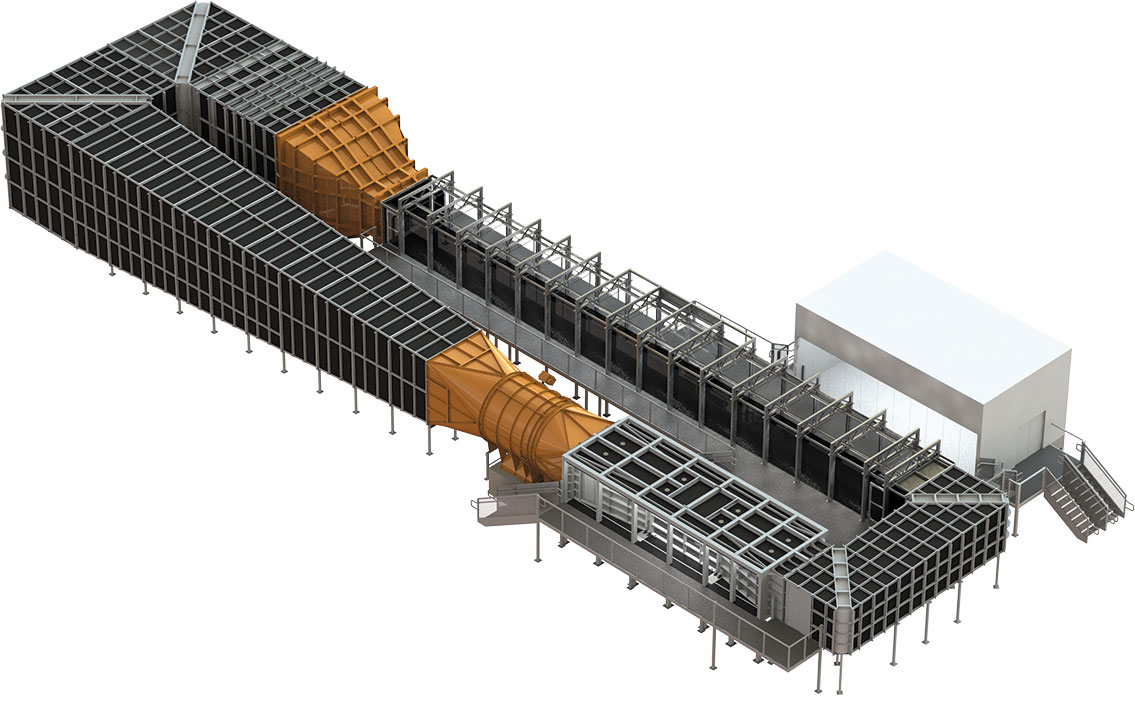
The Boundary Layer Test Section, where winds can reach 80 mph, is ideal for analyzing challenges in the automotive industry, such as drag reduction, noise prevention and windshield reliability. In BLAST’s Subsonic Test Section, winds can reach 115 mph, similar to a Category 3 hurricane or an EF2 tornado. In this range, for example, Griffith can examine his palm-frond prototype, or aircraft designers could test wind effects on airplanes using scale models.
BLAST is being integrated into curriculum and will be a key asset for students’ wind-related senior design projects. BLAST’s features are also likely to lead to new partnerships with national laboratories and other universities.
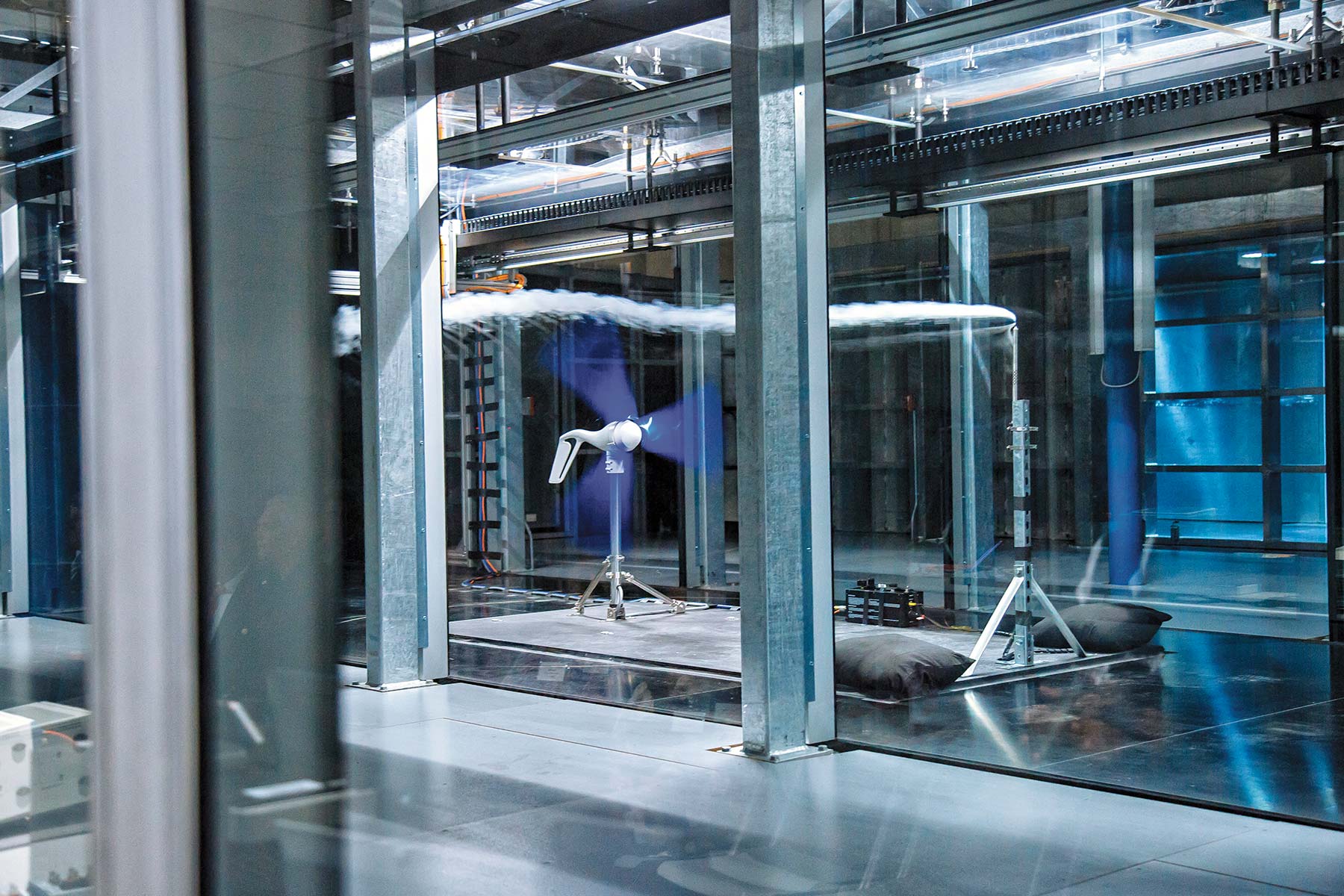
“With the experimental capabilities made possible by the BLAST wind tunnel, coupled with UT Dallas’ extensive capabilities in high-performance computing, we have that ideal blend of theory, experiment and simulation to take us to the next level of wind engineering,” said Dr. Richard C. Benson, president of UT Dallas and the Eugene McDermott Distinguished University Chair of Leadership.
“With our industry partners, we intend to build a progressively larger R&D program on the effects of wind on the natural and built environment,” he said.
It’s clear UT Dallas knows which way the wind is blowing.
“The time is right to leverage our investments in this field, to make Texas an even greater state for wind power in particular and wind engineering in general,” Benson said.